摘要:本文介紹了濕法噴注工藝的技術優(yōu)勢。聯(lián)合榮大濕法噴注工藝技術在煉鐵系統(tǒng)方面的一些技術成果,其中包括:高爐內(nèi)襯濕法噴注技術,濕法噴注技術在高爐煤氣封罩、上升管、下降管及重力除塵器的應用,濕法噴注技術在鐵溝上利用出鐵間隔對鐵溝進行噴注修補的開發(fā)及實踐應用。
關鍵詞 :濕法噴注技術,高爐內(nèi)襯,C沉積,可伸縮噴槍,溶膠結(jié)合,鐵溝噴補
1.濕法噴注工藝技術簡介
濕法噴注工藝(見圖1):不定形耐材經(jīng)定量加水(或液體結(jié)合劑)攪拌成砂漿狀澆注料,通過噴注機高壓輸送至噴槍口,與霧化的速凝劑混合噴出,在待噴面瞬間失去流動性而緊密粘附。該工藝解決了干法(或半干法)噴涂中水(或液體結(jié)合劑)與料無法充分攪拌有效混合的問題,超微粉和高效外加劑等新的耐材增強技術都得以在濕法噴注中實現(xiàn)。因此,濕法噴注料層可達到接近澆注料的指標性能;完全克服了傳統(tǒng)干法(或半干法)噴涂技術的種種不足。與傳統(tǒng)干法(或半干法)相比,其具有:
圖1 濕法噴注工藝示意圖
(1)配有分散減水劑等外加劑,液體結(jié)合劑加量少(僅為干法的一半)
(2)所噴出的為預攪拌砂漿澆注料,水或液體結(jié)合劑定量可控,材料性能均一、穩(wěn)定;
(3)反彈率小于5%,粉塵少;
(4)噴上去的料與設計的澆注料性能一致,氣孔率低、耐滲透侵蝕;
(5)臨界粒度10mm以上,結(jié)構強度高、耐磨性好;
濕法噴注工藝技術一經(jīng)實現(xiàn),就以其兼具噴涂的便捷高效和澆注的致密高強,逐漸成為不定形耐材施工的最主要方式。
聯(lián)合榮大自2010年開發(fā)高爐濕法噴注造襯以來,在實踐應用中不斷對濕法噴注技術進行探索、創(chuàng)新和改進,從工藝設備到材料取得了一系列的技術成果,F(xiàn)主要介紹榮大濕法噴注技術在煉鐵系統(tǒng)方面應用方面所取得的一些成果。
2.高爐內(nèi)襯濕法噴注技術
聯(lián)合榮大是國內(nèi)第一家成功實現(xiàn)高爐內(nèi)襯遙控濕法噴注的企業(yè)。自2010年成功應用以來截至2017年3月底,聯(lián)合榮大已經(jīng)在國內(nèi)外成功完成高爐內(nèi)襯噴注工程300多例,噴注料量近6萬噸。爐容積從350m³到4038m³不等。該高爐內(nèi)襯濕法噴注技術以其低反彈高壽命,得到鐵廠普遍認可,現(xiàn)已取代干法噴涂成為高爐內(nèi)襯維修維護的主要方式。
在高爐濕法噴注造襯技術方面,聯(lián)合榮大人不斷探索、創(chuàng)新和改進,無論在工藝裝備還是材料技術方面都走在了行業(yè)前面。圖2為針對不同工況所開發(fā)并應用的各式噴槍。
圖2 適應不同工況環(huán)境的各式噴槍
2.1 工藝裝備方面
機械手已完成三代改進,可伸縮噴槍(見圖3-1)能夠隨高爐直徑的變化遙控調(diào)節(jié);噴注施工過程可遠程視頻觀察(見圖4),客戶可在電腦或手機上隨時監(jiān)察現(xiàn)場的施工情況。新型的噴注設備能力達到平均每小時8-10噸,峰值可達18噸。圖3也顯示了噴注過程及噴注效果。工程記錄顯示,噴注過程無流淌無粉塵,實測反彈普遍低于5%(遠低于干法噴涂15~30%的反彈率)。噴注內(nèi)襯表面平整、材料密實。
圖3-1 適應不同工況環(huán)境的各式噴槍
2.2 材料方面
高爐內(nèi)CO導致耐火材料內(nèi)部C沉積,會對材料造成破壞,主要表現(xiàn)為崩裂及材料強度顯著降低,崩裂試樣如圖4所示。C沉積反應式如下所示:2CO=CO2↑+C
圖3 抗C沉積試驗前后試樣對比
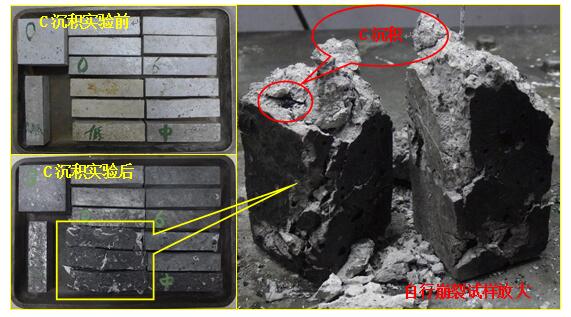
圖4 榮大高爐內(nèi)襯噴注手機遠程視頻圖像
尤其在有Fe存在的條件下,F(xiàn)e對上述反應能夠起到催化作用,使得該反應速率進一步提高。我們知道,耐火原料中不可避免會含有極少量Fe2O3,它們會和CO反應生成Fe,而這些Fe恰好充當了C沉積反應所需的催化劑。
Fe2O3+3CO=3CO2↑+2Fe
在高爐正常使用條件下,這些反應的發(fā)生不可避免。為了獲得抗C沉積性能優(yōu)異的高爐內(nèi)襯噴注料,我們對使用的每種材料做了抗C沉積性能的檢測,部分結(jié)果如圖5 所示:
圖5 幾種耐火原料CO環(huán)境C沉積導致增重對比
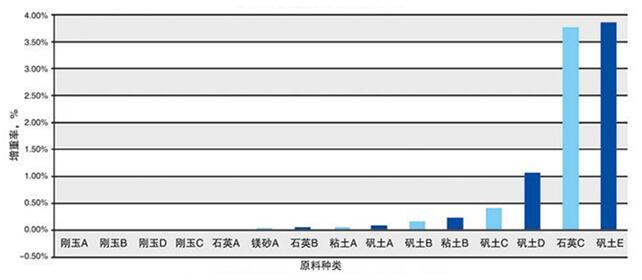
選擇抗C沉積性能優(yōu)異的材料作為噴注料主要原料,產(chǎn)品主要性能指標如表1所示。
表1 高爐內(nèi)襯噴注料技術指標
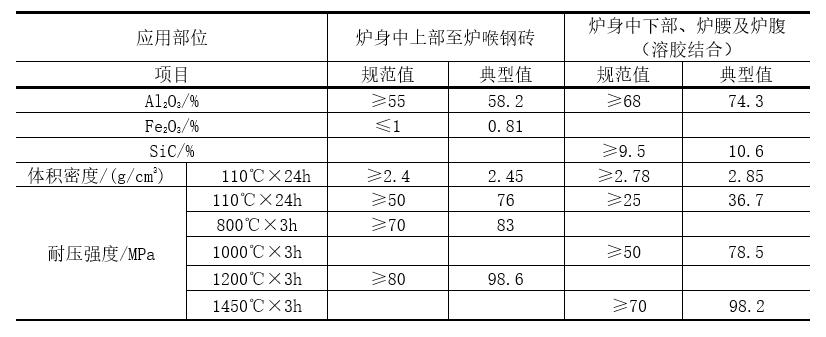
3 爐頂封罩、上升管、下降管及重力除塵器濕法噴注
由于濕法噴注技術外具有干法(或半干法)難以比擬的優(yōu)勢,聯(lián)合榮大在高爐內(nèi)襯濕法噴注的技術基礎上,還將該技術拓展應用到了高爐的爐頂封罩、上升管、下降管以及重力除塵器上。在通鋼、通才、漣鋼等廠家應用,同樣取得了良好的使用效果,得到了客戶認可好評。圖6為現(xiàn)場施工時檢查管道內(nèi)植筋掛網(wǎng)和噴注的照片,圖7為管道噴注完成。
圖6植筋掛網(wǎng)檢查、噴注現(xiàn)場 圖7 噴注完成
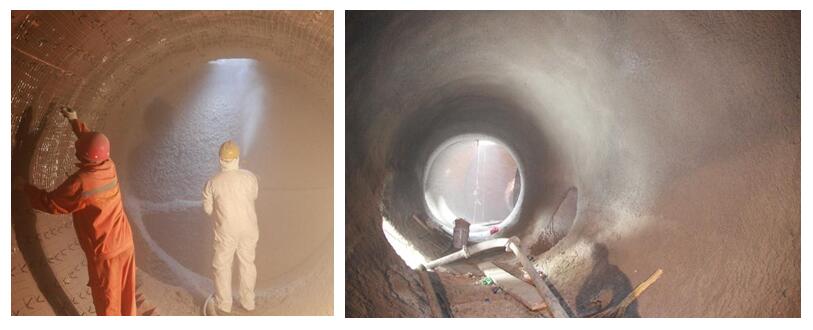
高爐爐頂封罩、上升管、下降管及重力除塵器噴注所用材料的理化指標見表2。
表2 爐頂封罩、上升管、下降管及重力除塵器濕法噴注料理化指標

4 鐵溝出鐵間隔濕法噴注維修
4.1 鐵溝濕法噴注技術研發(fā)
自聯(lián)合榮大2008年開始將儲鐵式出鐵溝技術應用于小高爐之日起,現(xiàn)中小高爐出鐵溝幾乎已全部改造為澆注的儲鐵式鐵溝。單鐵口高爐采用儲鐵式鐵溝,若要進行澆注維修(即使只局部落鐵點)至少也要7-8小時
因此,鐵廠必須進行休風;而休風就會影響高爐產(chǎn)量。為減少休風延長套澆周期,很多廠家曾利用出鐵間隔采用干法噴補方式對鐵溝落鐵點進行噴補。但干法噴補層最多僅能維持1-2天;噴補頻繁消耗巨大。濕法噴注技術可達近似澆注的性能,若采用濕法噴注的方式應能大幅延長噴補層的使用周期。另,考慮鐵溝的熱態(tài)維修,噴注后即要進行出鐵操作。常規(guī)水泥結(jié)合噴注料無水化結(jié)合時間,存在爆裂危險。因此,聯(lián)合榮大又開發(fā)了溶膠結(jié)合主溝濕法噴注料(性能指標見表3)。
表3 溶膠結(jié)合主溝濕法噴注料性能指標
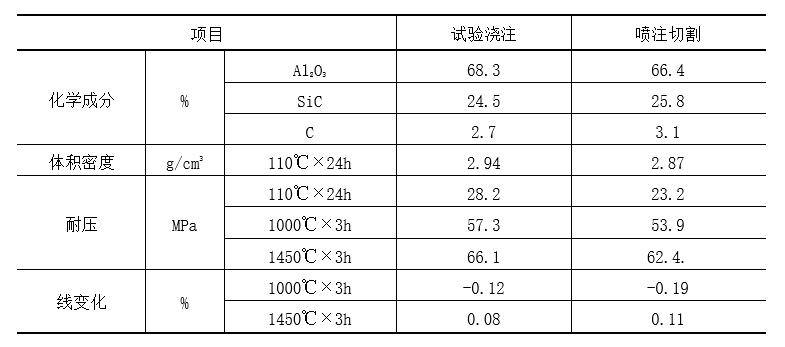
4.2 實踐應用
2012年,榮大公司在某鐵廠所承包的鐵溝已使用62天,落鐵點殘余厚度不足250mm,已達到合同約定的套澆周期。然而,鐵廠要趕產(chǎn)量不希望近期休風套澆。為此,榮大公司決定采用該鐵溝濕法噴注技術對該鐵溝的落鐵點進行噴注維護。
4.2.1 噴注維護過程
該高爐出鐵間隔為40-50min,為保證在正常出鐵間隔內(nèi)完成對落鐵點的噴注維護,噴注維護分兩次進行,每次噴注落鐵點的一側(cè)溝幫。圖8為鐵溝噴注維護現(xiàn)場,其施工工序如下:
(1)提前一爐將殘鐵眼燒開,再用炮泥堵上(以利于下一爐順利燒開,放凈殘鐵);同時所有設備及材料就位;
(2)在出鐵過程中完成燒放殘鐵工作,不占用出鐵間隔;
(3)對待噴注維護的一側(cè)落鐵點溝幫,采用氧氣對殘襯渣鐵進行吹掃,確保界面無渣鐵;用時15min;
(4)對該側(cè)溝幫進行濕法噴注維護, 25min完成噴注用料2.4噸;
(5)采用劈柴烘烤10min,后鉆開鐵口出鐵;
(6)在出鐵過程中,再次完成放殘鐵;而后利用正常出鐵間隔完成對另一側(cè)落鐵點溝幫的噴注維護。
圖8 鐵溝噴注維護現(xiàn)場
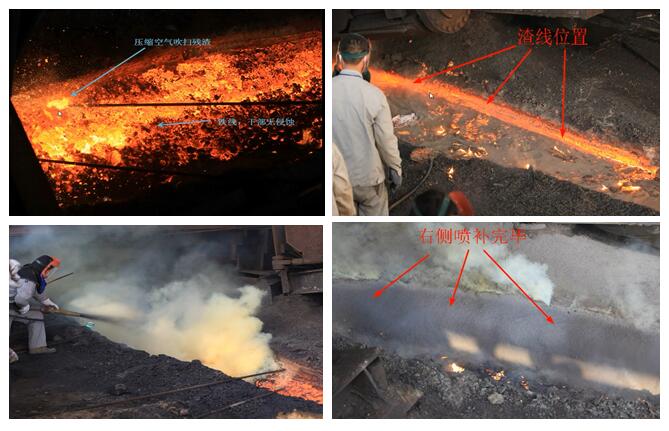
4.2.2結(jié)果及結(jié)論
通過兩次出鐵間隔完成落鐵點兩側(cè)溝幫的噴注維護,用料5噸,噴注維護厚度在350-400mm。噴注料與熱溝舊面粘附性好,噴注面致密,烘烤和出鐵過程無異常。使用31天,平均每天出鐵量2100t,噴注層損毀僅約為12mm/d。
鑒于如此好的噴注維護效果,在該鐵廠又連續(xù)進行了2次噴注維護,直至其計劃休風。至此該580m3高爐出鐵溝的大修周期達到131天,通鐵量達到了25萬噸。
后來榮大公司又在多條鐵溝落鐵點上進行了噴注修補驗證。采用濕法噴注修補技術,落鐵點噴補一次可使用20天以上,大大延長了套澆維修周期。
5 結(jié)語
濕法噴注技術以其兼具噴涂的便捷高效和澆注的致密高強,將成為不定形耐材施工的最主要方式。聯(lián)合榮大在濕法噴注技術上,從工藝設備到材料不斷進行自主研發(fā),開拓創(chuàng)新,現(xiàn)已開發(fā)出針對煉鐵、煉鋼、軋鋼等多領域,適合各種環(huán)境應用的濕法噴注裝備及材料。特別在濕法噴注技術在煉鐵系統(tǒng)應用方面,聯(lián)合榮大已當之無愧的成為了國內(nèi)濕法噴注技術的領軍企業(yè)。 |